It’s been 10 years since graphene was isolated by Geim and Novoselov at Manchester University in the UK. Today, graphene is available to purchase from a range of suppliers, you can buy equipment for growing it on wafers and foils and you can find graphene in products on the market, but the so-called “wonder material” is still in the early stages of its commercial journey.
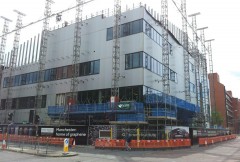
Taking shape: the National Graphene Institute at Manchester, UK. The state-of-the-art facility is due to open in March 2015, but staff will start moving in from October this year to begin proving out the building services.
“Short term applications will pave the way towards the principal uses of graphene,” Jani Kivioja, head of nanomaterials at Nokia, told attendees at LBC’s popular graphene conference series – now in its second year – which examines prospects for the 2D allotrope of carbon from an industrial perspective.
Early wins
TMR+ has reported graphene’s use as an additive to prevent drilling fluid degradation at high-temperature (see – Agensi Inovasi Malaysia and Graphene Nanochem team up to develop innovation hub), and there were other early wins presented at the event. Ready-for-market examples included a transparent conductive coating from TBA, which provides electrostatic discharge (ESD) protection to industrial lighting in explosive environments such as oil refineries or mining works (see TBA case study – PDF).
Graphene coatings are also of interest to Tata Steel, another attendee at the meeting. The firm sees the material’s barrier properties as an option for delivering anti-corrosion performance and extending the lifetime of its major products.
Plastic fantastic
Other areas with market potential include composite materials, where graphene’s high strength makes it an attractive additive. Its sheet-like form is beneficial during processing as graphene platelets flow easily over each other unlike carbon nanotubes, which can knot together and make composite mixtures much more viscous and harder to manage.
Karl Coleman, a professor at Durham University and one of the founders of Applied Graphene Materials, added that graphene is very good at reducing nitrogen permeation in thermoplastics, which is of interest in the packaging sector. Also, the low loading levels required preserve colour and transparency in the host material, which can be significant. Coleman is involved in Grapol, a four year project sponsored by EPSRC and partnered by Proctor and Gamble, and Dyson – two big consumers of thermoplastics.
As Coleman and others highlighted the effective integration of graphene into host materials is strongly dependent on surface functionalization, which is an area that suppliers such as Haydale are targeting with their plasma-treated graphene nanoplatelets. Surface functionalization also opens the door to the use of graphene in sensing applications, a sector that Nokia was upbeat about.
But will this be the killer application? For graphene to really take off there is a sense that it has to offer something different, something that no existing material on the market can do.
“Where I believe graphene can make a difference and be potentially disruptive is through its multifunctionality,” commented James Baker, who has moved from BAE Systems to become business director at the UK’s National Graphene Institute (NGI) – a £61 million facility under construction at Manchester University.
Graphene is unique in possessing so many record-breaking properties, but as we’ve mentioned previously on TMR+, designing multifunctional components to capitalize on this requires significant developer resources (see – Trajectories in translation: parallels between old and new materials) and pushes out the timeline for translating breakthroughs into the marketplace.
Facilities such as the NGI intend to bring academia and industry together under one roof to accelerate the commercialization of graphene from technology readiness levels 3-5 into early process validation. In September 2013, graphene CVD expert Bluestone signed up as the NGI’s first strategic partner and the building is on track to open in Q1 2015.
Reality check
Achim Hoffmann of IP group, a UK-based team of investors bridging the chasm between science and the city (financial district), reminded attendees that graphene is “technology before application”, which adds to the challenge. “We invest in businesses and value propositions – not materials,” emphasised Hoffmann. “Start-ups need to focus on who their customer is and how they address the market.”
Dispite the difficulties, a commercial landscape for graphene is emerging. Mark Rahn of MTI Ventures, who also spoke at the event, estimates that there are 23 countries (at least) with graphene companies. Europe hopes to be a major player through its Graphene Flagship, and across Asia there’s a wave of companies now making graphene in some shape or form – a point made by Kitty Cha of BASF and echoed by my colleagues at IOP China.
Device development
Seungmin Cho was representing Samsung Techwin at the workshop and talked about his team’s work on transparent electrodes. Using a graphene/PET film created by roll-to-roll processing, the group has demonstrated the manufacture of fully functional 4” touch screens – see ACS Nano 8 (2014) – but whether these devices make it into full production remains to be seen. “We need to find something that ITO cannot do,” Cho told the audience.
I got the impression from Shu-Jen Han’s presentation that graphene could be a hard sell in digital logic chips too. Han is a master inventor at IBM’s Yorktown Heights site in the US. The lack of a band gap in graphene means that devices are hard to turn off (in other words, you can write 1’s, but it’s tricky writing 0’s). There are ways of modifying the material to get around this, but from a commercial perspective the additional steps required are unattractive.
RF electronics on the other hand could be a much better match for the material. “For analogue devices you don’t have to turn the transistor fully on or fully off,” he explained. The IBM team has built a test circuit that can demodulate a digital signal carried over RF – see Nature Comm. 5, 3086 (2014). What’s more, the graphene chip was stable across a wide temperature range and up to high temperatures, which differentiates the device from versions made using traditional semiconductors.
Large organizations taking an interest in graphene include Lockheed Martin, which sees water security as a key part of its future business and believes that the 2D material could play an important role. To explain, Steve Sinton – principal chemist and Lockheed Martin fellow – introduced his team’s work on a perforated graphene membrane dubbed “Perforene”, which is seen as a promising platform for water purification (see datasheet – PDF). The work is early stage, but already the group has demonstrated that “Perforene” can reject salt ions from a test solution and copper from industrial wastewater, which has potential benefits in areas such as the electronics industry.
These are just a few highlights from what I found to be an insightful two days of talks and discussion. For further details on the event visit – www.graphene-applications-2014.com – and for more on graphene, check out the links below.
Related content on the web –
RESOURCES
Graphene: fabrication methods and thermophysical properties (Physics-Uspekhi)
Graphene: Applications and future uses (IOP)
Graphene coverage on nanotechweb.org
Graphene circuit ready for wireless (IBM Research blog)
COMPANIES
Aixtron # Applied Graphene Materials # Bluestone # Cientifica # Graphoid # Haydale # Ocsial # Perpetuus # Planartech #