Back in 2013, TMR+ hinted that the arrival of new feedstocks such as TPU 92A-1 – a flexible and durable thermoplastic – would make 3D printers a much more compelling proposition for product developers. Building on this, there are other factors to consider too –
Commercial additive manufacturing (AM) tools with multiple nozzles are paving the way for 3D-printed workpieces with tailored materials properties – the Objet500 Connex3 is a recent example.
In the lab, researchers are exploring AM designs that combine 3D and ink-jet printing, which bring additional functionality through the use of conductive and other custom inks.
3D printers such as the Freeformer from German production tool maker Arburg further extend the choice of starting materials by accepting granulated feedstock rather than specialized spools of pre-formed material that can turn out to be an expensive option for users.
“The mark-up on feedstock for 3D printing can be anywhere from 10 to 100 times the cost of the raw material, so the Arburg tool could be one way around that,” Anthony Vicari of Lux Research told TMR+. “It’s not just about cheaper materials though, there are other benefits,” he added, “you put your material through one less melt cycle, which should reduce product degradation.”
Vicari and his team have recently updated their projections for high-performance thermoplastics and see additive manufacturing as a growth area for this family of materials as 3D printing migrates from prototyping to manufacturing.
Process improvements are also making an impact.
For example, optics specialist LUXeXcel is using a slow curing technique to upgrade the performance of components printed from transparent resins for use in LEDs and other devices. The approach is designed to combat the formation of stepped features that would otherwise occur as a consequence of layer-by-layer fabrication.
Switching from plastics to ceramics, Vicari mentions Ceralink as another example. The US firm has developed a method for producing silicon carbide/silicon carbide composites using powder bed inkjet 3D printers.
The composite material is said to offer lighter weight, higher temperature performance, and higher wear resistance than nickel alloys and titanium alloys for aerospace jet engine components, and this highlights where 3D printing will have the biggest impact – when it brings something different to the process of translating new materials into devices.
Conventional volume manufacturing techniques such as injection molding will always be cheaper on a per unit basis, but this misses the point of 3D printing.
Commercial outlook
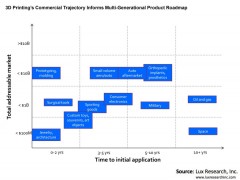
3D printing: applications and total addressable market (click on image to enlarge). Source: Lux Research
Some of the unique selling points of AM include customization for market segments such as orthapedic implants, prosthetics and sporting goods. Another positive is product assembly.
“With 3D printing you can often manufacture several parts as one piece, which reduces construction costs, but can also save on regulatory filings too,” Vicari points out.
The on-demand nature of AM means that 3D printing could help firms to reduce product inventory (as well as tooling storage) and lower warehouse costs. It also offers supply-chain security in sectors such as space and defence, by enabling on-site production of replacement parts.
Related links –
TPU 92A-1 datasheet (PDF via materialise.com)
Stratasys’ Big Announcement — Multi-colour, Multi-material 3D Printing with the New Objet500 Connex3 (3dprintingindustry.com)
Printing Batteries – new inks and tools allow 3-D printing of lithium-ion technology (MIT Technology review)
3D Printed Silicon Carbide: Ceralink’s Novel Production Process for Jet Engine Material (luxresearchinc.com/blog)